11/03/2024
In June 2023, Mercedes-Benz unveiled a new concept car named the Vision One-Eleven. While paying homage to the iconic C111 from the 1970s, the Vision One-Eleven concept provides a glimpse into what the future of electric vehicles (EVs) might look like. In particular, the concept features ‘new’ type of electric motor – an axial-flux motor. The manufacturer of this motor (a spin-out from Oxford University) claims that, in contrast to the traditional radial-flux electric motors powering our EVs today, their axial-flux motor “requires one third of the space, one third of the weight and delivers double the torque density.” This is, of course, a big statement.
Axial-flux motors are already commercially present in industry, in applications where their low rpm high torque capability is utilised, for example in lift systems and wind turbines. Following developments in design, materials, and manufacturing, we could be on the precipice of their widespread implementation in the automotive sector. Although contrary to the Vision One-Eleven, that widespread implementation is more likely to be in the lightweight, low cost, low speed sector such as small motorbikes.
Axial-Flux Motors (AFMs) vs Radial-Flux Motors (RFMs)
Permant-magnet synchronous-motors (PMSMs) feature ubiquitously in the EV market. PMSMs can be divided into two main categories based on their topologies: RFMs and AFMs. In RFMs, the magnetic flux is perpendicular to the shaft, whereas in an AFM, the flux travels parallel to the motor rotation axis. The upshot of this is that the two types of motor are noticeably different in shape. In essence, due to the arrangement of the windings in relation to the flux, AFMs have a compact disc design and RFMs have a comparatively bulkier cylindrical design.
Although RFMs are bulkier than AFMs, they require a significantly reduced volume of permanent magnets and are far more straightforward to construct. This leads to a noticeably lower manufacturing cost, allowing for easier implementation into electric vehicles. This is largely why they are the most common type of PMSM used in the EV market today.
AFMs offer a higher power density, high torque-to-weight ratio, and greater design flexibility than their radial counterpart. These advantages share a symbiotic relationship – they all relate to the size and weight of the motor. These benefits are ideal, but the technology has only seen its recent application in the automotive industry at the absolute highest end. The high complexity and precision required in the manufacturing of AFMs mean that they are currently only viable in low quantity, high value models, created by brands such as Koenigsegg, McClaren, and Ferrari.
The goal of many manufacturers of AFMs will be to reduce manufacturing cost to the point where they are economically viable for OEMs that mass produce hybrids and solely electric vehicles. Another obstacle that manufacturers and designers must overcome is to solve the inherent heat dissipation problem in AFMs, in order for them to become more robust and durable. This, in our opinion, makes it more likely that the first widespread adoption will be in the small motorbike sector where heat dissipation is less of a problem.
Efficiency Bonus
It will benefit the average consumer if AFMs become available for everyday vehicles. Vehicles using AFMs will often have increased range over a RFM for a given power rating – this benefit is realised in two ways. Firstly, the topology of AFMs allow for a more efficient use of magnetic flux, meaning there is reduced energy loss, resulting in higher efficiency. Secondly, AFMs offer an improved power-to-weight ratio over RFMs, largely due to their compact design which requires less overall material. In an EV, a motor with reduced weight will improve range in an immediate sense. However, further weight savings are available due to a compounding effect on the rest of the vehicle, leading either to a further range enhancement, or to a reduction in the required battery capacity for a given range requirement.
Compounding Effect
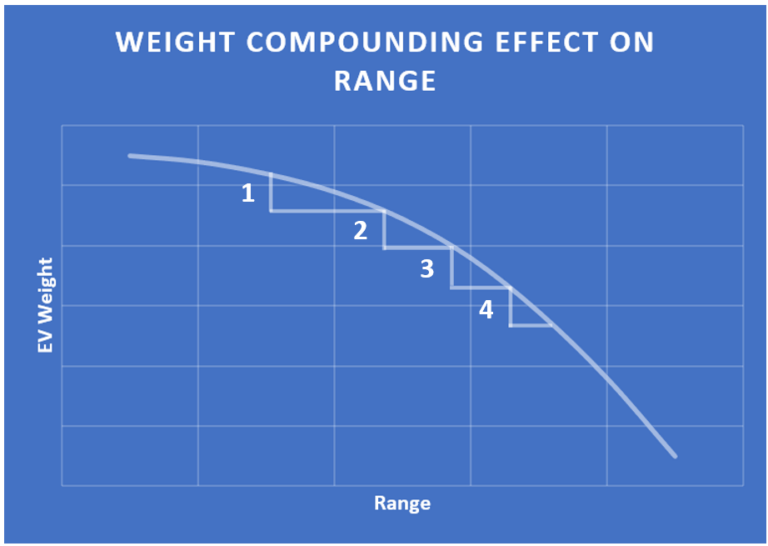
Imagine a standard electric vehicle, equipped with the typical technology one would normally expect to see. From here, we can visualise how the compounding effect arises when an RFM is replaced with an AFM. Reference will be made to each of the numbers in Fig. 1 – each number represents a stage of weight reduction.
Point 1 – The introduction of the AFM results in an immediate increase in range due its lower mass and increased efficiency over the RFM. The immediate range increase is approximated between 5-10%.
Point 2 – If the range is maintained, a smaller battery can be used. In doing so, battery weight would be reduced proportionally to the range increase provided by the AFM – in this case 5-10%. Batteries are typically the heaviest components in EVs, so a 5-10% reduction in battery weight is significant and has a drastic effect on the rest of the car.
However, now that the car is lighter, less energy is required to move the vehicle because it has less inertia. A lighter car can now also operate with a less powerful motor. The lighter car will use energy from the smaller battery more sparingly and thus increase the range. This particular point may take a couple of re-reads as it appears paradoxical at first glance.
Point 3 – Other mechanical and load bearing components of the car do not need to withstand the same forces. A car with a lighter battery and motor does not need the same bulky chassis, it can use smaller brakes, etc…
Point 4 – The, now lighter and more efficient, car, requires smaller electrical subsystems such as: converters, inverters, thermal management systems, etc. This further contributes to weight loss, culminating in a final range increase for the vehicle.
As you can see, looking at Fig. 1, the range benefit of a lighter and more efficient motor extends far beyond the motor itself.
Sustainability
Thanks to the compounding effect, production of EVs may in turn become more sustainable. A lighter EV requires less material, therefore less energy is required to source the material, so less CO₂ and other harmful gases will be emitted as a by-product during manufacture. EVs, in use, will be more sustainable, due to their enhanced efficiency realised by the weight compounding effect – initiated by implementation of the AFM.
Next Steps
The global demand for EVs is constantly on the rise. Automakers will aim to meet this demand and provide vehicles that appeal to the masses. Gone are the days where branding, design, and performance of a vehicle are the sole considerations of a prospective customer. A modern-day customer, contemplating what vehicle to purchase next, will increasingly give ‘weight’ to the efficiency and sustainability of a vehicle. Automotive manufacturers that successfully implement AFMs may dominate the market for years to come, as their EVs will possess enhanced efficiency and perhaps sustainability over their RFM-using rivals.
This article is for general information only. Its content is not a statement of the law on any subject and does not constitute advice. Please contact Reddie & Grose LLP for advice before taking any action in reliance on it.