10/05/2024
Additive manufacturing, commonly referred to as 3D-printing, is a production process of directly depositing material onto material, usually in layers, until a component is formed. Once cutting-edge, the technology has matured somewhat, with desktop polymer 3D-printers widely available to hobbyists for a few hundred pounds.
A 2020 report issued by the European Patent Office (EPO) declared Europe a “global hub for innovation in 3D printing” [1]. This report followed a quadrupling in rate of patent applications in the broader additive manufacturing field between 2013 and 2018, growing ten times faster than the average growth of patent applications at the EPO over the same period.
The implications this technology has for the production of metallic components however are of particular interest to engineers and industrialists.
Traditional metal processing techniques such as casting or moulding come with geometrical constraints, such as limiting the production of complex or hollow parts, and require significant upfront investment in a dedicated mould. Milling or turning on the other hand allows for variation between subsequent components, but at the cost of often significant material waste.
It is therefore clear why metallic additive manufacturing, promising next to no tooling costs, rapid prototyping, and minimal material waste, is seen as such an attractive offering.
Historical background
Metallic additive manufacturing can be traced back to the middle of the 20th century. US patent application US 3596285 A filed in 1969 disclosed a so called ‘Liquid metal recorder’. Figure 1 below shows the arrangement in which a stream of molten bismuth-lead alloy (18) is deflected by a magnetic field generated by a magnet (30). Upon striking a surface (16), the molten stream solidifies.
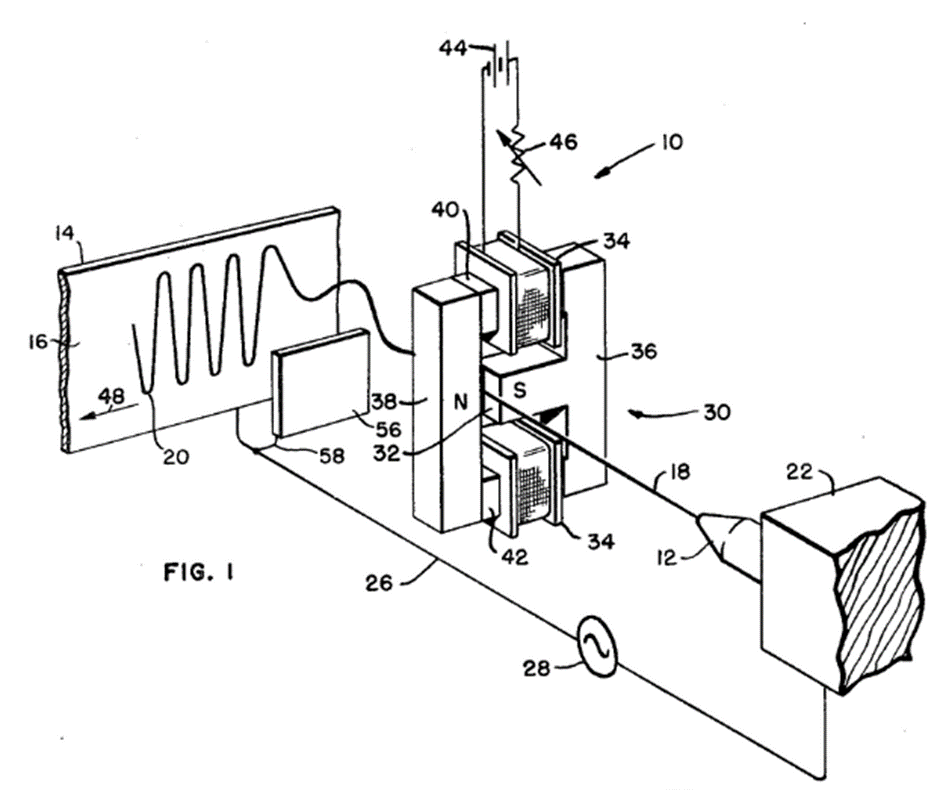
This patent application somewhat understates the practical applications of such a novel technology however, and only gives the example of recording market transactions in a stockbroker’s office.
More modern additive manufacturing of metals encompasses a wide range of techniques; many involving the fusion of a metallic powder precursor. A common one is that of selective laser melting (SLM). German patent application DE 19649865 A, filed back in 1996, describes the technique illustrated below.
A focused laser beam melts a cross-sectional area of a powder bed, before a successive powder layer is applied on top, and the laser melts a successive cross section. The heat generated by the laser allows for complete melting of the powder, and hence the formation of highly dense metallic bodies. A schematic of the technique is shown below.
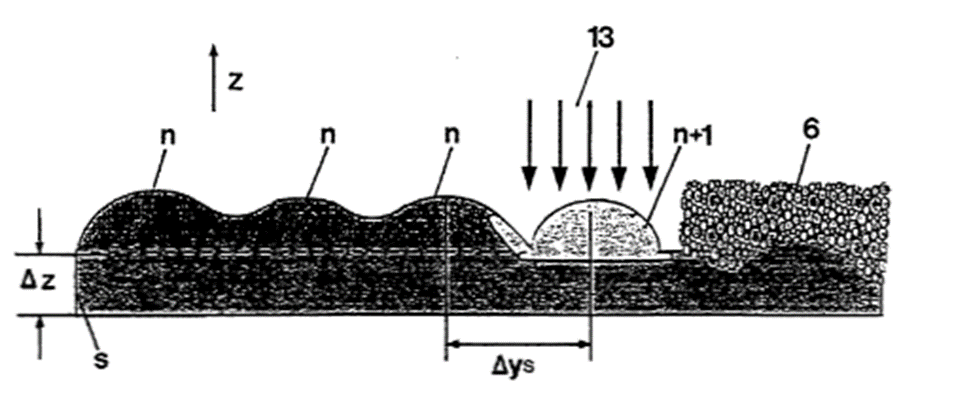
Present-day trends
Though both of the above metallic additive manufacturing techniques were published in the 20th century, we can look at how more recent interest in the technological field has varied over the past decade.
The below graph illustrates recent European patent application filing rates for three broad classes of metal processing techniques: additive manufacturing of metallic powders; casting & moulding; and turning, milling & other metal removal techniques.
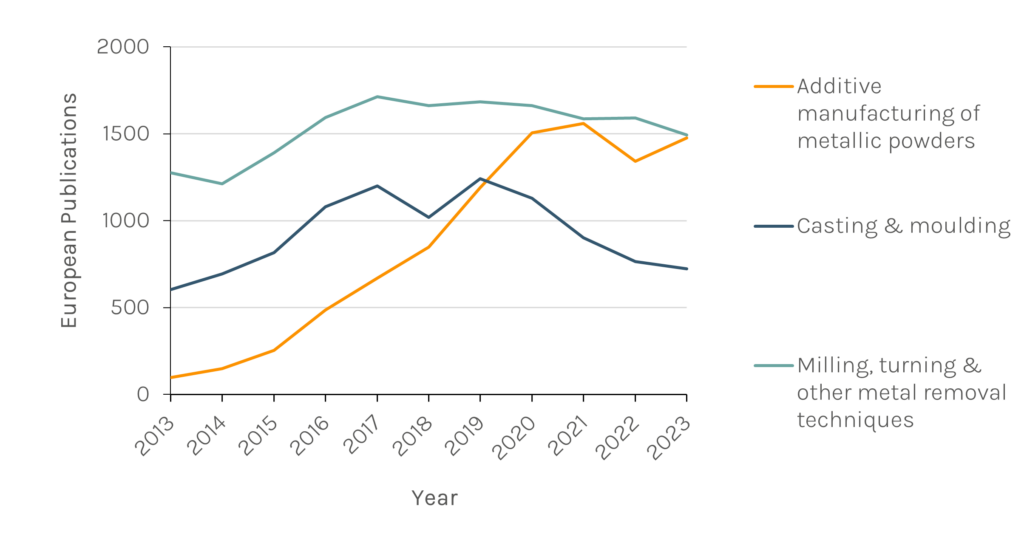
Whilst the filings for the exemplary ‘traditional’ techniques of casting & moulding and turning & milling have remained rather steady over the ten-year period shown, filings for additive manufacturing of metallic powders show a marked increase, before levelling off in more recent years. So much so, that the filing rate for additive manufacturing of metallic powders is now on par with the filing rates of these traditional metal processing techniques.
This shows that interest of additive manufacturing of metallic powders has significantly grown over the past decade, but not at the expense of the development of traditional metal processing techniques. This is perhaps an indication that additive manufacturing is seen by European industry as a complementary technology, rather than a revolutionary one which will replace these traditional techniques outright.
Looking at filing trends beyond Europe however, we see a different picture. In China, patent publications for traditional metal processing techniques are at a much greater scale than in Europe.
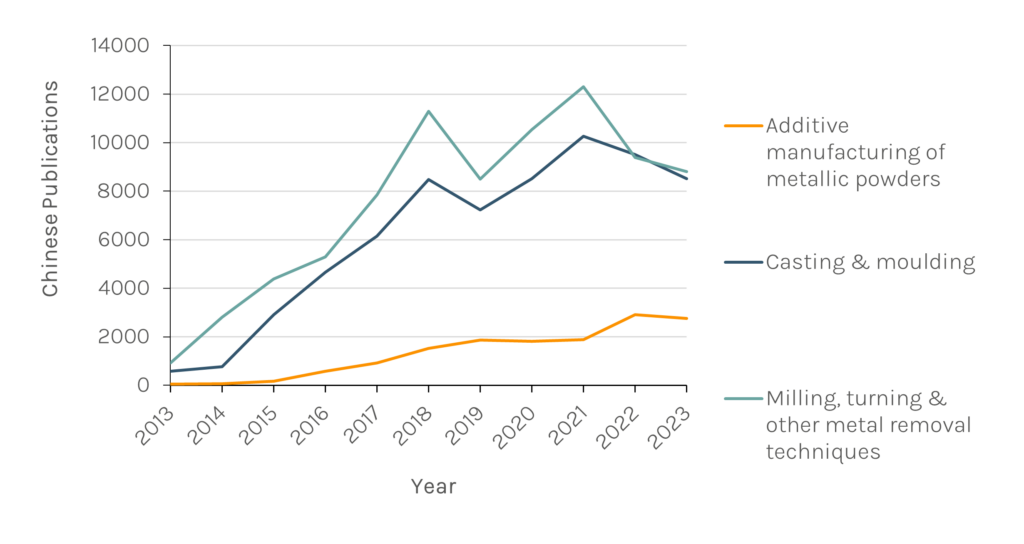
With significant heavy industry and metal processing located in China, this focus on traditional techniques may not come as much of a surprise. For context, as of 2021, China is reported to both produce and use over 50% of steel worldwide [2].
The below pie charts summarise the corresponding cumulative patent publications since 2018 for five major patent filing authorities: Europe, the US, China, Japan, and Korea.
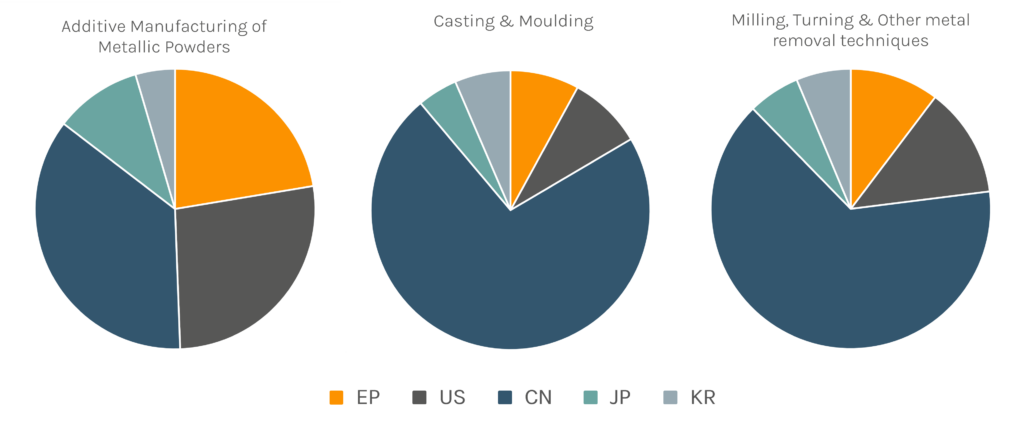
In the more traditional metal manufacturing techniques such as casting and machining, the scale of Chinese publications clearly dominates other jurisdictions. The 45,000 Chinese casting & moulding publications and 53,000 Chinese milling, turning & other metal removal technique publications both comprise around two thirds of the publications in these technical fields from the five authorities.
Recent publications in additive manufacturing of metallic powders are spread much more equally across jurisdictions, however. Additive manufacturing is particularly applicable to prototyping and research & development, and these techniques may be performed with a on a smaller scale and with a smaller footprint. This contrasts with more traditional metal processing where more developed supply chains, large factories and production lines are often necessary. Therefore this filing trend is understandable, as patent protection outside the major industrial jurisdiction of China is viewed as of equal commercial importance.
Interest in metallic additive manufacturing has soared in recent years, and the technology has the potential to significantly supplement current research and development efforts, particularly outside of traditionally industrial jurisdictions. If you need assistance or advice to protect your additive manufacturing innovations, then please do get in touch with one of our attorneys at Reddie & Grose.
This article is for general information only. Its content is not a statement of the law on any subject and does not constitute advice. Please contact Reddie & Grose LLP for advice before taking any action in reliance on it.